Мы – уазовцы. Александр Лащ: аппаратчик-гидрометаллург участка выщелачивания
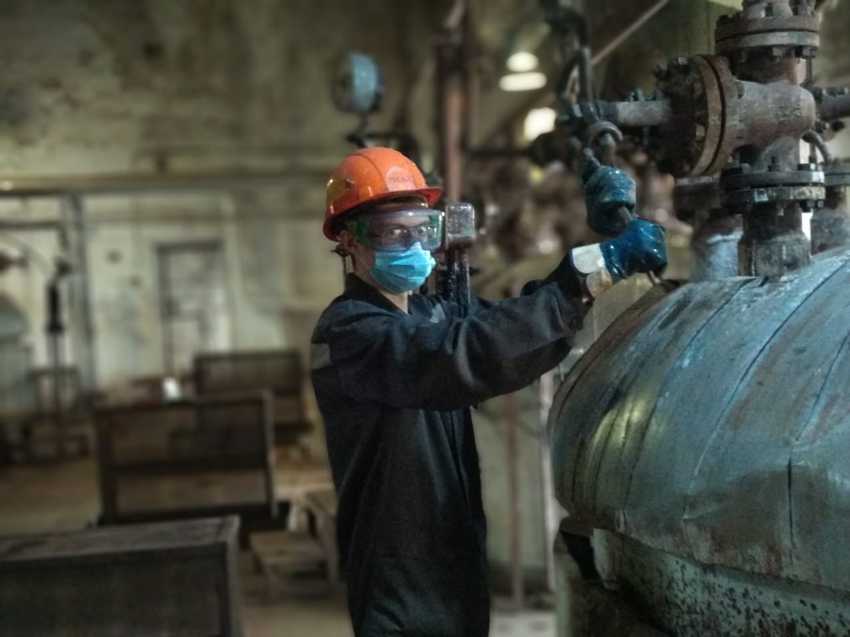
Уральский алюминиевый завод – одно из крупнейших промышленных предприятий Каменска-Уральского. Порядка четырех тысяч человек – представителей более 100 профессий – трудятся на промплощадке УАЗа, выпуская глинозем высшего качества. Цикл материалов «Мы – уазовцы» посвящен людям, представляющим основные профессии глиноземного производства: аппаратчикам-гидрометаллургам, машинистам вагоноопрокидывателя, мельниц, перегружателей, компрессорных и насосных установок, дробильщикам, агломератчикам, лаборантам и многим другим, кто является его неотъемлемой частью.
Производственная цепочка глинозема начинается в цехе подготовки сырья (ЦПС). За первоначальную подготовку руды и ее доставку на склад отвечают бункеровщики, дробильщики и транспортерщики. Далее по линиям транспортеров сырье отправляется на склады, где за подготовку шихты – смешение извести с рудой – и дальнейшую ее подачу по цепочке отвечают машинисты крана.
После шихта загружается в бункер питателя тяжелого типа, предназначенного для непрерывной подачи шихты в молотковую дробилку. Дробленый боксит по транспортерам подается в приемные бункера отделения мокрого размола. После этого шихта из бункеров попадает на транспортеры и доставляется по ним в мельницы. Из отделения мокрого размола ЦПС сырая пульпа передается в цех выщелачивания и сгущения (ЦВС). Здесь она попадает в мешалки сырой пульпы. За работу мешалок, автоклавных батарей и другого оборудования отвечают аппаратчики-гидрометаллурги участка выщелачивания.
Трудовой путь Александра Лаща, аппаратчика-гидрометаллурга второго участка ЦВС, на Уральском алюминиевом заводе начался в 2018 году, когда он пришел в ЦВС после окончания Каменск-Уральского политехнического колледжа.
За три года работы на предприятии Александр зарекомендовал себя профессионалом, отлично знающим свое дело. Исполняет обязанности мастера смены. Вместе с коллегами разрабатывает и внедряет улучшения и кайзены, участник корпоративной программы подготовки кадрового резерва «БС 250+».
- В должностные обязанности аппаратчика-гидрометаллурга участка выщелачивания входит обеспечение бесперебойной работы основного и дополнительного оборудования: мешалок сырой пульпы, насосов, подогревателей, автоклавных батарей, сепараторов, агитаторов, предохранительных устройств - рассказывает Александр Лащ.
Производственный цикл на участке полностью автоматизирован: все процессы, от скорости вращения центробежных и поршневых насосов до уровня пульпы и давления в сепараторах, управляются при помощи автоматики. Аппаратчики-гидрометаллурги осуществляют дополнительный контроль ее работы, а также следят за целостностью сосудов и трубопроводов пара, работающих под давлением. В случае выхода из строя какой-либо части оборудования именно аппаратчик-гидрометаллург проводит первоначальный анализ причин поломки и либо передает информацию специалистам, либо, если имеет компетенции и допуски, проводит мелкий ремонт ремонт сам.
- Сырая пульпа приходит с первого или четвертого участка ЦПС и попадает в мешалку, где происходит ее усреднение и предварительное обескремнивание, – то есть поддержание необходимой, однородной, консистенции. Если пульпу не перемешивать, то твердые фракции начнут выпадать в осадок, забивать насосы – производственный процесс остановится, - отмечает Александр Лащ.
Далее насосами сырье подается в подогреватели сырой пульпы, где доводится до температуры в 168 градусов Цельсия. После этого пульпа поступает в автоклавную батарею.
Каждая батарея состоит из семи автоклавов, соединенных последовательно трубопроводами. Первые два называются греющими. В них из буферного сосуда подается пар, поступающий от Красногорской ТЭЦ, посредством которого происходит подогрев пульпы до 228-230 градусов, благодаря чему запускаются химические процессы.
Именно в автоклавах проходит процесс выщелачивания: под воздействием высоких температур и щелочной среды происходит перевод боксита (сырой бокситовой пульпы) в раствор щелочи гидроксида алюминия (алюмината натрия) - вареной пульпы.
Автоклавы – основное оборудование глиноземного производства. С 2015 года на УАЗе в рамках долгосрочной программы повышения надежности глиноземного производства проводится замена автоклавов. Программа рассчитана до 2033 года. Постоянная модернизация производства и совершенствование технологических процессов – принципы, заложенные основателем компании Олегом Дерипаска. Сегодня они реализуются нынешними руководителями компании.
Из автоклавной батареи вареная пульпа под давлением в 23,5 атмосферы выгружается в сепараторы. В сепараторе происходит отделение пара от пульпы. За счет этого понижается давление и температура вареной пульпы. Отделенный пар возвращают в производственный процесс – в подогреватели сырой пульпы.
Вареная пульпа отправляется в агитатор разбавления, где ее разбавляют до необходимой концентрации. Далее раствор подается на участок сгущения, где за производственный процесс также отвечают аппаратчики-гидрометаллурги. Работе этого участка будет посвящен следующий материал цикла «Мы – уазовцы».
Андрей Васильев